机械加工作为现代制造业的核心环节,通过多种工艺将原材料转化为精密零部件,其技术流程与应用场景紧密关联行业创新与效率提升。
一、机械加工的核心概念解析
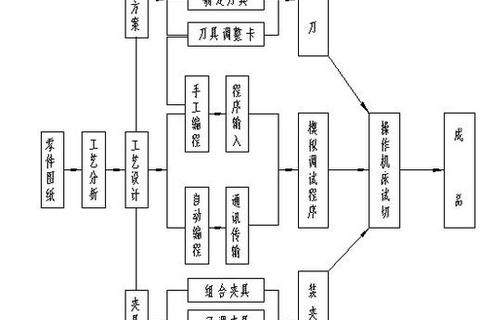
1. 定义与分类
机械加工指通过物理手段改变原材料形状、尺寸或性能的过程,主要分为两大类:
切削加工:利用刀具对材料进行切削(如车削、铣削、钻孔)
成型加工:通过压力或热能改变材料形态(如铸造、锻造、冲压)
2. 基本原理
加工过程遵循“材料去除”或“形态重塑”原则,需平衡精度、效率与成本。例如,切削加工需控制刀具转速与进给速度,而成型加工需精确计算温度与压力参数。
二、机械加工的技术流程拆解
1. 加工准备阶段
设计图纸审核:确认尺寸公差与表面粗糙度要求
设备与工具选择:根据材料硬度选择机床类型(如硬质合金刀具适合加工不锈钢)
夹具安装:确保工件固定稳定,避免加工偏移
2. 加工实施阶段
粗加工:快速去除多余材料(效率优先)
精加工:通过精细切削或研磨达到设计精度(精度优先)
实时监测:使用传感器检测刀具磨损与加工振动
3. 后处理与质检
去毛刺与清洁:采用化学抛光或人工打磨
尺寸检测:使用三坐标测量仪或激光扫描设备
性能测试:包括硬度测试与抗疲劳试验
三、机械加工的典型应用领域
1. 汽车制造
案例:发动机缸体加工需同时满足轻量化(铝材)与高强度(热处理工艺)
痛点解决:采用组合加工技术减少工序切换时间
2. 航空航天
特殊需求:钛合金零件加工需控制切削温度防止材料氧化
技术创新:五轴联动数控机床实现复杂曲面加工
3. 医疗设备
精密要求:人工关节加工表面粗糙度需低于Ra 0.4μm
材料挑战:医用不锈钢与陶瓷的生物相容性处理
四、提升机械加工效率的实用建议
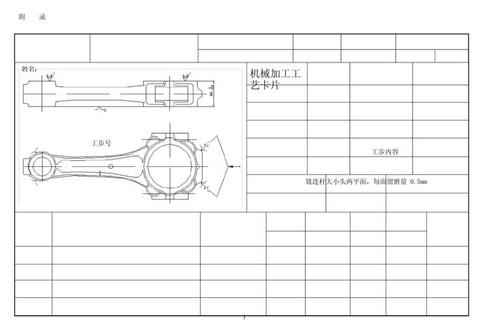
1. 工艺优化策略
参数组合实验:通过正交试验法确定最佳切削速度与进给量
刀具寿命管理:建立磨损预警系统,减少意外停机
冷却液选择:水基冷却液适合铝合金加工,油基液适合铸铁
2. 成本控制方法
批量加工规划:合并相似工序降低夹具更换频率
废料回收利用:金属碎屑可熔炼再生(回收率可达85%)
能源监控:安装智能电表统计机床空载耗电量
3. 技术升级路径
入门级建议:传统机床加装数显装置提升读数精度(改造成本低于2万元)
进阶方案:引入CAM软件实现从设计到加工的数字化衔接
前沿技术:探索增材-减材复合加工技术(3D打印与切削结合)
五、行业发展趋势与应对策略
1. 智能化转型
实施步骤:
1. 部署物联网传感器采集设备状态数据
2. 构建加工参数数据库实现工艺经验数字化
3. 通过机器学习预测刀具剩余寿命
2. 绿色制造要求
合规性实践:
使用生物降解切削液替代矿物油
通过拓扑优化设计减少材料浪费率
申请ISO 14001环境管理体系认证
通过系统化理解机械加工的技术逻辑与应用场景,企业可针对性优化生产流程。建议中小型企业优先聚焦单一领域的工艺突破,例如专精高精度小批量加工,逐步构建技术护城河。对于操作人员,定期参加G代码编程或数控系统维护培训,将显著提升岗位竞争力。
相关文章:
文章已关闭评论!