在流程化管理的现代企业中,标准操作程序(SOP)是确保效率与质量的基石。它通过规范化操作流程,降低人为失误风险,已成为制造业、医疗行业、服务业等各领域提升竞争力的重要工具。
一、标准操作程序的核心价值解析
标准操作程序本质是将隐性经验转化为显性知识的过程。通过将重复性工作分解为可量化的步骤,企业能够实现三个关键目标:
1. 降低操作风险(美国食品药品管理局研究显示,标准化流程使医疗事故发生率下降43%)
2. 提升工作效率(制造业案例显示流程标准化后产能提升25%)
3. 保障质量稳定(ISO认证企业质量波动幅度减少60%)
典型应用场景包括:
新员工上岗培训体系
高风险操作流程控制
跨部门协作接口规范
突发事件应急响应机制
二、SOP构建的五大核心模块
1. 流程节点拆解
采用流程图工具(如Visio)可视化呈现
标注关键控制点(CCP)与风险阈值
示例:餐饮行业中央厨房的食材验收流程包含7个检查节点
2. 操作标准量化
温度控制:精确到±1℃范围
时间管理:设定合理波动区间(如5分钟缓冲期)
质量参数:定义可测量的验收标准
3. 责任矩阵设计
| 岗位角色 | 执行责任 | 监督责任 | 复核责任 |
|||||
| 操作员 | √ | | |
| 班组长 | | √ | |
| 质检员 | | | √ |
4. 文档管理系统
版本控制(实施三级修订制度)
权限管理(设置部门级访问权限)
更新机制(每季度定期审查)
5. 培训验证体系
理论考核(80分合格线)
实操评估(设置模拟场景)
定期复训(每半年强化关键环节)
三、落地实施的四个关键阶段
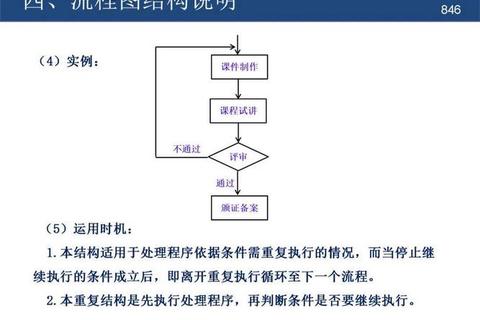
第一阶段:需求分析
运用5W1H法确定编制范围
收集历史事故数据(重点关注重复性问题)
访谈岗位专家(记录操作细节差异)
第二阶段:文档编制
采用分级目录结构(主流程→子流程→操作要点)
嵌入智能提示(在关键步骤添加注意事项弹窗)
配置多语言版本(适用于跨国企业)
第三阶段:试点运行
选择典型部门/产线进行测试
记录执行偏差(建立问题日志)
设置改进周期(2周快速迭代)
第四阶段:全面推广
分批次培训(每批次不超过20人)
建立双轨运行机制(新旧流程并行1个月)
配置流程督导员(前3个月全程跟进)
四、持续优化的三大机制
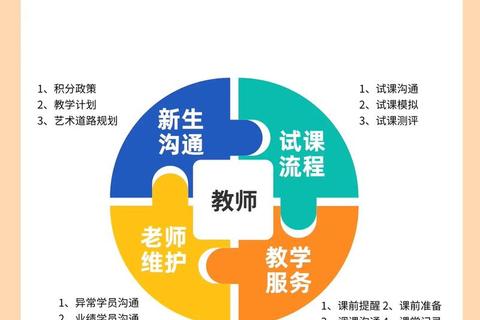
1. 动态反馈系统
设立线上建议平台(每月收集有效建议超50条)
开展质量圈活动(跨部门改进小组)
实施改进积分制度(与绩效考核挂钩)
2. 数据监控仪表盘
关键指标可视化(如流程遵守率、异常发生率)
设置自动预警阈值(触发邮件提醒功能)
生成月度分析报告(含趋势预测)
3. 版本迭代策略
微小调整(在线文档即时更新)
中度修改(季度集中发布)
重大变更(启动专项修订项目)
五、常见误区规避指南
过度细化陷阱:单个SOP文档控制在10页以内
形式主义风险:每季度进行有效性评估(剔除3项无效条款)
更新滞后问题:设置文档失效提醒(超期未更新自动警示)
执行偏差处理:建立三级纠偏机制(现场纠正→系统分析→流程优化)
企业实践表明,有效实施的SOP体系能在6-12个月内带来显著改善:某汽车零部件厂商通过优化装配SOP,使产品不良率从3.2%降至0.7%,同时减少培训周期40%。关键在于建立PDCA循环机制,将标准制定、执行监督、检查改进形成闭环,最终实现运营质量的持续提升。
相关文章:
文章已关闭评论!