“一班三检”制度是企业安全管理中一项基础性、持续性风险防控机制。它通过班前、班中、班后三次系统化检查,将隐患消灭在萌芽阶段,保障作业全流程安全可控。本文结合实践案例,解析三次检查的核心流程、实施意义及落地难点,为企业提供可操作的优化建议。
一、制度框架:三次检查的流程拆解
“一班三检”以班组为单位,覆盖生产全周期,形成“预防-监控-复盘”的闭环管理链条。
1. 班前检查:风险预控的“第一道闸门”
班前检查在作业开始前完成,目标是消除前置性隐患,具体包括:
人员状态排查:确认班组成员精神状态是否良好,是否饮酒或带病上岗(如某供电公司要求班前会观察员工面色、反应速度)。
防护装备核查:检查安全帽、防护服、绝缘工具等是否齐备且符合标准(例如某化工厂要求防护服耐腐蚀性检测记录每日更新)。
设备与环境预检:
机械设备是否完成保养并处于停机状态;
作业区域是否存在杂物堆积、地面湿滑等风险;
应急通道是否畅通,消防器材是否在位。
实用建议:
使用标准化检查表(如《班前检查10项清单》),通过勾选“是/否”提高效率。
班组长需在5-10分钟内完成检查,避免因赶工而流于形式。
2. 班中检查:动态监控的“安全雷达”
班中检查贯穿作业全过程,重点关注实时风险与操作合规性:
设备运行监测:通过温度、振动等参数判断设备异常(如某钢厂采用红外测温仪实时监控轧机轴承温度)。
人员行为纠偏:制止违章操作(如高空作业未系安全带、带电检修未挂牌)。
环境风险预警:监测粉尘浓度、有毒气体泄漏等环境变化。
难点突破案例:
某汽车制造车间引入智能巡检系统,员工佩戴AR眼镜扫描设备二维码,系统自动调取检查标准并记录数据,班中隐患发现率提升40%。
3. 班后检查:隐患清零的“收尾工程”
班后检查强调现场复位与交接规范:
工完场清:工具归位、废料清理,避免遗留尖锐物或易燃物(如某建筑工地要求钢筋头必须当日回收)。
设备交接:填写《设备状态交接单》,标注故障待修部位(如某电厂规定未完成检修的阀门需悬挂“禁用”标牌)。
数据记录:通过移动端APP上传检查结果,生成电子台账供追溯。
二、价值驱动:制度实施的多维意义
1. 事故预防:从“被动应对”到“主动防御”
统计显示,80%的生产事故源于未及时发现的隐患。“一班三检”通过高频次检查,将风险识别窗口前移。例如某煤矿推行该制度后,顶板脱落事故率下降62%。
2. 意识提升:培养“全员安全员”文化
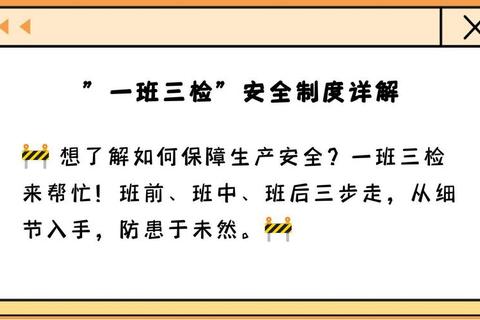
操作层:员工在反复检查中强化风险敏感度(如某石化企业员工自主发明“管线法兰松动预警贴”)。
管理层:班组长通过检查数据分析,优化资源配置(如调整高危岗位轮班频次)。
3. 管理增效:降低隐性成本
直接成本:某制造企业统计显示,因设备故障导致的停产损失减少23万元/月。
间接成本:工伤赔付、事故调查等费用同比下降57%。
三、落地难点与破解策略
难点1:检查流于形式
症状:员工为赶进度,5秒完成“打钩式检查”。
对策:
推行视频记录检查过程,随机抽查真实性;
设置“隐患发现奖励基金”,鼓励深度排查。
难点2:跨班次责任推诿
症状:交接班时设备故障责任界定不清。
对策:
使用区块链存证技术,确保交接记录不可篡改;
建立“隐患共担机制”,上下两班联合签字确认。
难点3:检查标准模糊
症状:不同员工对“设备正常”的理解存在偏差。
对策:
制定可视化操作指南(如用绿、黄、红标签表示设备状态);
每季度组织“标准校准培训”。
四、进阶建议:构建长效运行机制
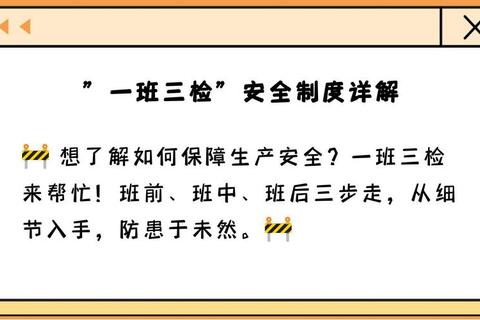
1. 工具升级:
部署物联网传感器,实时监测设备振动、温度等数据;
开发AI语音助手,提示检查要点(如“请确认配电箱接地线紧固”)。
2. 考核优化:
将“隐患整改率”纳入KPI,权重不低于产量指标;
实行“安全积分制”,积分可兑换培训或休假。
3. 文化渗透:
开展“安全微剧场”,员工演绎典型隐患场景;
设立“安全里程碑”(如“连续1000天无事故”),增强集体荣誉感。
“一班三检”绝非简单的三次打卡,而是需要技术、制度、文化三方协同的体系化工程。企业需根据行业特性细化标准(如化工企业增加危化品泄漏检查项),并通过持续迭代检查工具与方法,让安全真正成为生产的“默认配置”。
相关文章:
冲红是什么意思_概念解析与常见操作流程详解2025-04-19 14:40:02
文章已关闭评论!